Relay innovation enhances solar PV inverter performance
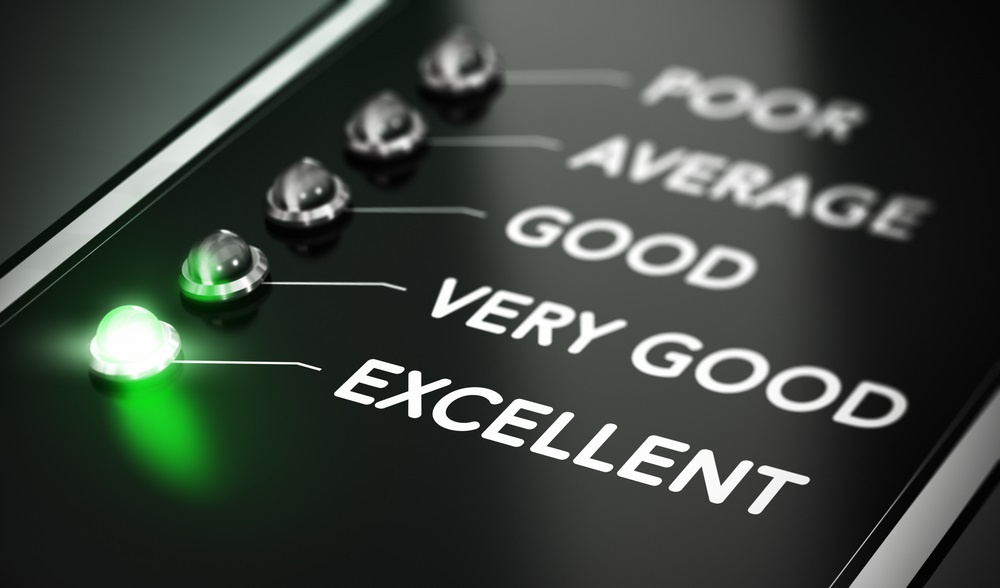
In recent years, solar PV inverters have seen a considerable uptick among domestic and commercial electricity users, offering a convenient way of supplementing electricity from the grid. As well as reducing energy bills, they are also a highly sustainable solution. Indeed, it is estimated that installing solar inverters in every house in the UK would provide up to 60 percent of total electricity consumption. Moreover, based on the UK’s climate it could even potentially generate a surplus against domestic demand between the months of April and September.
This makes solar PV an attractive proposition for those who are looking to make their properties more sustainable, while also reducing their energy bills. It can also help to achieve significant progress in facilitating the transition towards a greener grid. More recently, the growing adoption of electric vehicles (EV) has been a catalyst for greater interest in solar PV as an integrated power solution for EV chargers, providing additional charging capacity and greater efficiency while harnessing clean energy.
Getting the technology to a point where solar PV is effective, efficient and affordable, has required decades of innovation. Systems not only need to provide the means to safely connect and disconnect the panels as required, but also convert the DC output into the AC at the correct voltage. Relays and switches are central to the design of such systems, and relay manufacturers like Omron have not been slow to innovate and address the needs of this rapidly growing sector.
Compactness vs heat performance
Heat dissipation underpins almost every facet of relay design. Heat is fundamentally bad for both the efficiency and longevity of electronic devices and components, and so the more that temperatures of components can be reduced, the better. Complicating matters is the fact that, as inverter output power and functionality increases, dissipating generated heat effectively becomes more difficult. Relays are a current switching device, and so can generate lots of heat, potentially damaging themselves and components around them.
Meanwhile, solar PV inverter manufacturers require their relays to be increasing smaller, while regulations on component and device energy performance are only becoming more stringent. If too many heat-generating components are too close together, or not adequately cooled, then this will compromise reliability and safety. As such, innovative approaches are required to squeeze every last drop of efficiency out of the system.
Reduced contact resistance
In a typical relay, contact resistance is key to managing heat dissipation. Omron’s G9KA relay utilizes an especially pure form of silver as its contact material. Silver has the highest electrical conductivity and lowest contact resistance of all known metals. Indeed, silver is in fact the standard against which all other metals are measured on these criteria. In practice, this means that the G9KA has a heat performance five to ten times greater to that of most other products on the market.
The G9KA also utilizes a twin contact structure, which compared to a single contact reduces the current per contact to almost half, and in doing so generates less heat. In a single contact configuration, contacts must be a minimum of 4mm apart to achieve the required performance. With a twin structure, this gap can be reduced to 2mm, allowing the same performance in a smaller footprint due to the smaller magnetizing coil, and reduced physical space required. Each contact has high contact pressure, which when combined with low initial contact resistance, multiple connection paths and high conductivity, results in superior efficiency and performance. In turn, this allows relays to be used in more compact applications, while still accommodating an adequate contact gap.
Life in the field
Solar PV inverters typically have a lifespan of five to ten years, and in some cases up to 15 years. Relays are not a component that can be easily replaced, and so it is vital that any relay component is sufficiently robust to outlast the inverter itself, and require zero maintenance during its operational life. Standard IEC 62109 also specifies that the performance of the relay must not drift over time. This is a challenge, as solar inverters can be installed outdoors exposed to the elements all year round.
A typical inverter can go through several switching cycles in a single day, most obviously between day and night, but also during periods of shade and planned or unplanned downtime. This can add up to tens of thousands of electrical operations in a typical relay’s lifetime. Manufacturers must run rigorous testing to not only ensure its longevity, but also calculate its footprint and power budget at every point of its operational lifecycle.
In Omron’s case, these calculations are done for the first 30,000 electrical operations, at which point the G9KA typically demonstrates only negligible drift in contact resistance of around 0.05 milliohms, far outperforming comparable products. With two relays in series for redundancy, the likelihood of failure in normal operating conditions is practically nil, with minimal change in performance from the beginning to the end of the inverter’s operational life.
Safety and longevity
Even a small change in efficiency can make a big difference to the amount of heat generated. A load terminal and surrounding surface temperature above 115˚C will prematurely age components, while temperatures even higher than this can increase the risk of eventual arcing and even catastrophic failure. Internal forced air conditions typically deployed help to maintain temperatures, but a relay must also be part of a good overall system design to ensure that heat dissipation across all components is managed effectively.
On the DC panel side and input to solar PV inverters Omron’s G9KB uses arcing control technology, utilizing permanent magnetism to stretch or elongate the arc. When stretched in the direction of the current flow, the arc can be extinguished more easily, improving system safety while reducing the likelihood of catastrophic failure.
In summary
PCB relay designs have opened up exciting new avenues for the evolution of solar PV technology. PCB systems can help to reduce design cycles, and allow engineers to harness greater flexibility to improve their products. It also helps designers to achieve higher outputs within smaller designs. Against the backdrop of the drive towards net zero, relay manufacturers like Omron are helping to accelerate the transition towards a cleaner grid.
By Steve Drumm, Strategic Marketing Manager, Omron Electronic Components Europe bv